En la industria, reducir costes de producción no se trata de fabricar más barato, sino de hacerlo mejor. Se trata de eliminar ineficiencias, ajustar recursos y optimizar cada paso del proceso sin afectar la calidad del producto ni la capacidad de entrega.
Muchas pymes industriales pueden mejorar su rentabilidad actuando sobre pequeños detalles que, acumulados, suponen un ahorro considerable. Desde RRM Consultoría ayudamos a identificar esos puntos clave y a implantar mejoras reales, sostenibles y adaptadas a cada fábrica.
En este artículo reunimos las estrategias más efectivas que aplicamos en el día a día para ayudar a nuestros clientes a producir más, con menos.
Eliminar procesos duplicados
Muchas fábricas repiten tareas sin darse cuenta: entradas de datos en papel y luego en ordenador, comprobaciones manuales que ya están automatizadas, aprobaciones innecesarias. Detectarlos y eliminarlos libera tiempo y reduce errores.
Mejorar la planificación de compras y producción
Una mala planificación provoca compras urgentes (más caras), paradas por falta de material y sobrecostes por exceso de inventario. Con un ERP bien configurado, es posible ajustar los pedidos al ritmo real de fabricación y optimizar los lotes de producción.
Formar al personal en productividad
No todo es cuestión de software. A veces, una formación práctica en uso de herramientas, organización de planta o tiempos de trabajo mejora notablemente el rendimiento y reduce tiempos muertos.
Controlar al detalle las mermas
Registrar y analizar cada rechazo, residuo o pérdida permite actuar sobre las causas: materiales defectuosos, fallos de máquina, errores humanos... Las mermas no eliminadas acaban lastrando los márgenes.
Automatizar tareas repetitivas o administrativas
Desde los partes de trabajo hasta los pedidos de reposición, muchas tareas se pueden automatizar con herramientas como Odoo o Sage. Esto reduce errores, mejora la agilidad y permite dedicar el tiempo a tareas de más valor.
Tener KPIs claros y visibles
Sin indicadores es difícil mejorar. Cada fábrica debería tener métricas clave como coste por unidad, productividad por operario, tasa de merma o desviación de costes. Y lo más importante: que esos datos estén visibles y actualizados en tiempo real.
Errores comunes al controlar los costes
Intentar controlar los costes sin una estrategia clara puede acabar generando más problemas de los que se pretende resolver. En RRM Consultoría nos encontramos con estos errores con bastante frecuencia en pymes industriales que han intentado mejorar sus márgenes sin el enfoque adecuado:
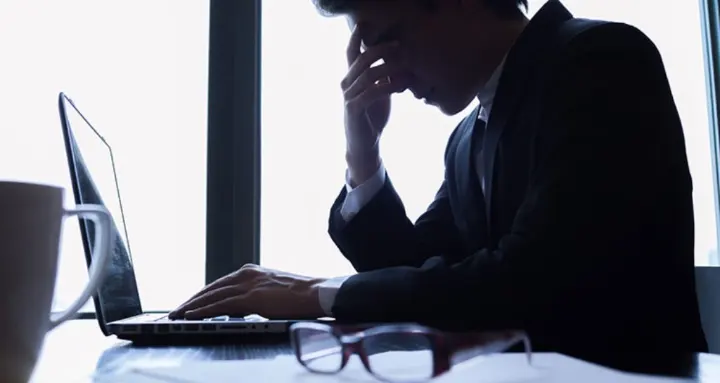
Depender de hojas Excel desactualizadas
Excel puede servir para empezar, pero cuando los datos no se actualizan en tiempo real o se gestionan en múltiples versiones, el margen de error crece. Además, el tiempo invertido en mantener esas hojas se dispara y los análisis pierden fiabilidad.
No revisar los escandallos de productos
Muchos escandallos están basados en precios antiguos, procesos obsoletos o materiales que ya no se usan. Si no se actualizan de forma periódica, el cálculo del coste por unidad será erróneo... y con él, los precios de venta.
Medir solo al final del mes
Controlar los costes de forma mensual no es suficiente. Las desviaciones deben detectarse lo antes posible, idealmente en tiempo real. Si se espera al cierre mensual, las pérdidas ya están consolidadas y corregir es más complicado.
No involucrar a los equipos de planta
El personal de producción es quien mejor conoce los procesos y los problemas del día a día. Si no se les escucha ni se les forma en control de costes, cualquier mejora quedará incompleta o se aplicará mal.
Instalar un ERP sin adaptarlo al modelo productivo
Un error frecuente es implantar un sistema estándar sin tener en cuenta las particularidades de cada fábrica. Cada empresa tiene su ritmo, su estructura y sus necesidades. Si el software no se adapta, no se usará bien... y el proyecto fracasará.
Cómo lo hacemos desde RRM Consultoría
En una pyme industrial, no hay margen para el ensayo y error.
El tiempo es limitado, los recursos también, y las decisiones deben ser rápidas pero bien fundamentadas. Por eso, en RRM Consultoría aplicamos una metodología práctica y contrastada, diseñada para obtener resultados desde el primer mes.
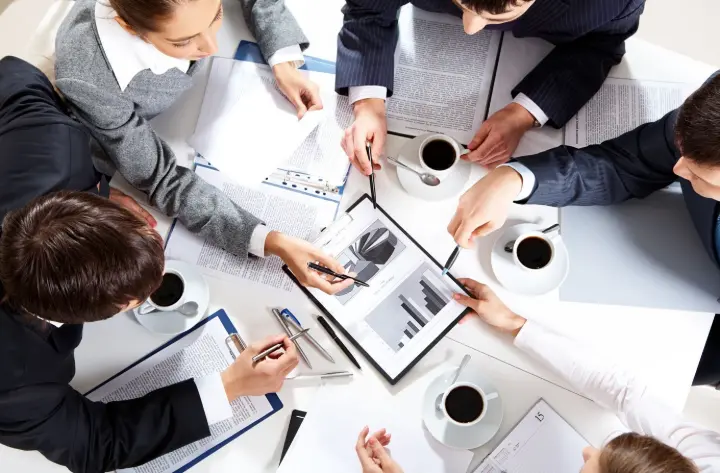
Estos son los pasos que seguimos:
Diagnóstico técnico y económico inicial
Analizamos la situación real de la empresa, detectamos las fugas de coste y evaluamos el impacto económico de no actuar.
Mapeo de procesos de producción
Documentamos cómo se fabrican los productos, qué recursos se utilizan, qué procesos se duplican o generan errores, y dónde se pierden datos.
Implantación de herramientas ERP adaptadas
Seleccionamos el sistema más adecuado (Odoo, Sage o uno propio) y lo configuramos según las necesidades de cada planta. Nada de soluciones genéricas ni plantillas estándar.
Formación de operarios y responsables
Capacitamos al equipo para que entienda cómo utilizar el sistema, cómo registrar los datos correctamente y cómo tomar decisiones a partir de ellos.
Soporte técnico y mejora continua
Una vez implantado, seguimos acompañando a la empresa con asistencia diaria, evolución del sistema y análisis de nuevos indicadores.
Gracias a nuestra experiencia en el sector industrial, podemos detectar con rapidez dónde se están perdiendo recursos y cómo optimizar la producción de forma sostenible.
Sectores donde más impacto tiene el control de costes
No todas las industrias tienen los mismos retos, pero sí comparten una realidad: cuando se controlan bien los costes de producción, los márgenes mejoran y la empresa gana estabilidad.
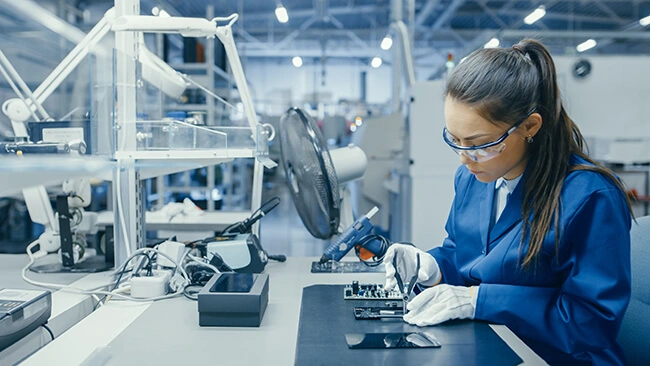
Desde RRM Consultoría hemos trabajado con pymes de sectores industriales muy diversos, ayudándoles a reducir gastos ocultos y tomar decisiones basadas en datos. Estos son algunos de los sectores donde el impacto es más notable:
- Fabricación de maquinaria: donde los procesos suelen ser complejos, con múltiples fases, proveedores y materiales específicos.
- Producción agroalimentaria: especialmente sensible a la gestión de mermas, trazabilidad y normativa.
-
Metalurgia y siderurgia: con altos consumos energéticos y dependencia de materias primas volátiles.
- Embalaje y packaging: donde controlar el desperdicio de materiales y los tiempos de máquina es clave.
-
Equipos eléctricos y electrónicos: donde el coste por unidad debe estar muy ajustado para competir en precio sin perder calidad.
Hemos acompañado a pymes de estos sectores a implementar sistemas de control que les han permitido ahorrar miles de euros al año y ganar visibilidad total sobre su proceso productivo.
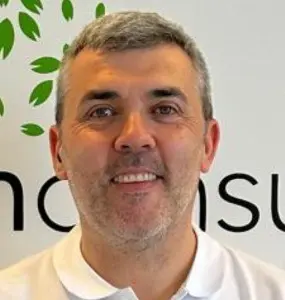
Ramón Rodríguez - CEO RRM CONSULTORÍA
Ramón Rodríguez, fundador y CEO de RRM Consultoría, cuenta con una amplia experiencia en el sector, incluyendo su paso por Sage Group. Desde el Centre d'Empreses Industrials de Can Roqueta, ha liderado la digitalización de procesos y la optimización de costes para sus clientes, impulsando el crecimiento de la empresa mediante colaboraciones y oportunidades de networking.